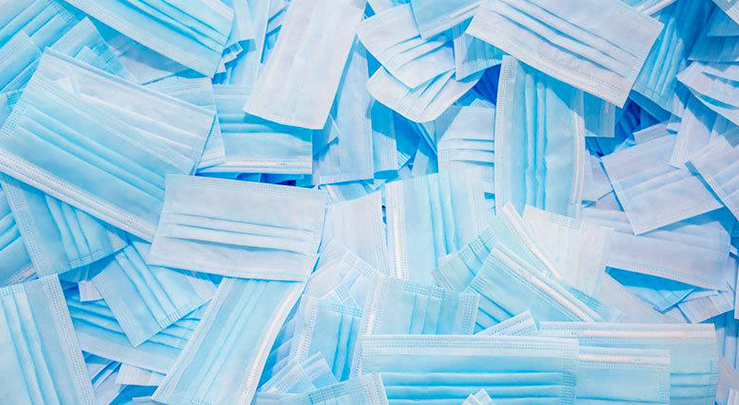
Mask workshop
At the beginning of 2020, a large-scale outbreak of a new type of Covid-19 occurred in China. By April, the epidemic has covered the world. Isolation at home and safe travel have become a rule that everyone follows. In this urgent matter, masks have become an indispensable item, and there is even a shortage of demand.
With the increase in the demand for masks, more and more manufacturers have invested in the production of masks. The large-scale production of masks that work overtime day and night makes the mask machines too difficult to bear. The main problem is that the heating problem of the ultrasonic transducer. Generally it has the following three reasons:
1.
A.The parts to be welded will heat up or the substances acted on by ultrasonic waves will heat up;
B. The Molds/welding heads/die heads/tooling will heat up after works for a long time;
C. The amplitude modulators/horns will heat up after working for a long time; Accumulate, and then pass to the transducer.
2. The transducer itself cannot convert all high-frequency electrical energy into mechanical energy, and part of the power loss is also converted into heat.
3.A slow increase in the temperature of the transducer will cause changes in its own performance, which will gradually deviate from the better matching state of the transducer, which will result in a gradual decrease in the performance of the piezoelectric ceramic wafer, and cracks and damage in severe cases. This process makes the performance state of the transducer worse, which in turn leads to a faster temperature rise, which is an irreversible evil cycle state. Therefore, conditions must be created so that the transducer can be cooled well, air-cooled at room temperature, and better is to use cold air.